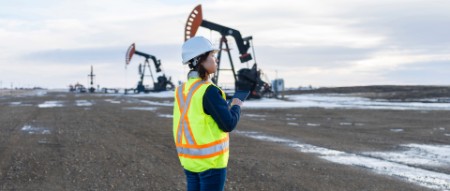
The better the question
When time can cost millions, how do you roll back the clock?
Communication and collaboration are key, as blockages in the flow of information can be costly.
To survive the current market upheaval, oil and gas companies realize they must do more with less. In an environment where prices are low and demand is flat, efficiency and cost control are critical. Increasing production by getting every drop possible from existing wells provides value that goes straight to the bottom line.
An integrated oil company (IOC) approached the EY energy team for help in optimizing production in one of their basins. Production operations are a complex endeavor, with significant levels of cross-functional coordination: typically, 8 to 10 disciplines work in tandem to achieve production goals. Collaboration across functions, and often across assets, is therefore critical.
Because most communication is still handled by email and phone, formal and complete record-keeping and recall is uneven. Project teams lacked full awareness, leading to siloed decision-making. Collaboration was hindered because not everyone had access to the most up-to-date data or the latest decisions.
There were thousands of wells in this basin, with an average downtime of about 10% to 25% per well. Each time a well went offline, it was costly. For the company’s high-producing wells, the loss in revenue could be as much as US$250,000 to US$500,000 a day. Given current downtime averages, there were millions of dollars of lost revenue each year in that basin alone.
Traditionally, each of the company’s production engineers working in that basin were tasked with the oversight of dozens of wells. To manage production, they routinely scanned outputs from various sensors — looking at trend lines in pressure, flow rate, temperature and well test data to identify potential problems. This surveillance data drives both long- and short-term optimization and recovery decisions. Work orders to solve immediate well problems are then created and executed with the help of lease operators and trades.
Given the amount of data available, and the manual task of reviewing it across various applications or spreadsheets, prioritization of repairs is a challenge. It can be difficult to pinpoint exactly what problems are most serious and where the lease operator should focus time and effort. As a result, the operator may spend time on small-volume wells with major problems while ignoring large-volume wells with minor problems. This approach is not efficient and leads to significant lost production. And often, well downtime is missed altogether due to the manual aspect of scanning multiple reports and spreadsheets.
The better the answer
A single source of truth
Centralizing data boosts efficiency and helps future planning.
The EY Digital Energy Enablement Platform (EY DEEP) team, consisting of industry experts, including petroleum engineers, collaborated with the company to create a bespoke solution that would provide a single source of centralized data.
EY DEEP not only pulls in information from various siloed systems — including oil and gas third-party production systems — but also alerts the company to production deviations in real time via Microsoft’s analytics capabilities. Once the company is alerted, the field service module is able to use its GPS functionality to dispatch vendors or production supervisors to address the issue. Production supervisors can now also see past alarms and how previous issues were resolved. Having both real-time and historical information in one place allows the company to address issues more efficiently, reduce downtime and perform preventive maintenance based on prioritization logic.
The better the world works
Supporting better decision-making by breaking down data silos
By providing the right tools, engineers and operators can excel.
In addition to boosting production operations efficiency, the common data model enabled the company to reuse specific well data in other parts of the upstream value chain. By combining production data with reservoir estimations, EY DEEP identified underperforming wells and subsequently coordinated efforts to address the issues and loop the information back into future planning. This helped the company manage asset performance and maintain visibility of key performance indicators in real time to inform both tactical and strategic longer-term decisions.
Using EY DEEP, engineers and operators were able to more than double the number of wells they managed, allowing companies to drill and produce more without hiring new staff. And the rapid access to insights and awareness, which gave each engineer and operator the ability to do more in less time and expand their oversight capabilities, made it possible.
In the wider world, oil remains critical not only to the global economy but also to the daily lives of billions of people. It is of vital importance that oil and gas companies are given the necessary tools not only to update their systems to bring their business models into today but also to adapt to survive tomorrow. EY DEEP is helping oil and gas companies operating in major basins continue to serve those customers by substantially shortening the time it takes to turn natural resources into energy that powers businesses, homes and automobiles. At the same time, it helps oil and gas companies create safer, more productive and more rewarding job experiences for employees, while reducing the risk of negative environmental impacts by helping minimize errors in key upstream processes.
The team
Contact us
Like what you’ve seen? Get in touch to learn more.